The Nautical Institute draws lessons learned from an incident in which a crew member was injured when an air hose disconnected unexpectedly and whipped his face.
A chemical tanker was discharging in port and two crew members were working to top-up the air pressure in the lifeboat air supply cylinders. One crew member was in the compressor room and operated the compressor while the other was in the lifeboat to connect/disconnect the air hose to the cylinders and validate the pressure. The crew member in the lifeboat was aware of the procedure but had never carried out the task before. There was no visual contact between the two crew members and communication was maintained by means of portable VHF radios.
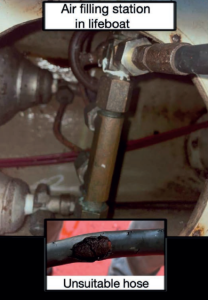
All three cylinders were topped-up to a pressure of 200 bar. Then, after confirmation from the crew member in the lifeboat that the air cylinder valve was closed, the crew member at the compressor drained the air hose at the compressor end. When the pressure at the compressor gauge indicated 0 bar, he informed the crew member in the lifeboat by radio.
The crew member in the lifeboat also confirmed that the pressure gauge inside the lifeboat was zero. He then started to disconnect the air hose. When the air hose was almost completely disconnected, he heard air escaping from the filling valve; a small pressure had apparently built up in the supply line. He bent forward to check whether the cylinder valves were properly closed. At that moment the hose came off the connection and whipped his face. The crew member at the compressor heard shouting for help over the radio. He went immediately to the lifeboat and saw the victim was bleeding near his right eye. First aid was given and the victim was sent to a shore hospital.
The investigation found, among other things, that some air had re-pressurised the hose. This pressure was enough to initiate a whipping movement when the hose connection released of its own accord, having been nearly unscrewed by the victim.
Due to the lay-out of the air supply system, the person manipulating the air cylinder valves is in a vulnerable position in close proximity to the pressurised air hose. Although the filling hose was found to be in unsatisfactory condition, this was not a contributing factor to the accident. It should have been checked, discarded and replaced with an adequate hose by the crew members prior to commencing the job.
Lessons Learned
- Gases under high pressure are a potential hazard and risk assessments should adequately capture the risks and present reasonable mitigating practices for workers.
- High pressure components, such as air hoses, should be regularly inspected and unsparingly relegated if found in any way worn.
Eye protection at all times and for all tasks; ideally it should become as ubiquitous as hardhat use.