NTSB published a report on March 23rd, 2022, concerning a fire that was reported on the commercial fish processor Aleutian Falcon while the vessel was docked for repairs at the Trident Seafoods shipyard in Tacoma, Washington.
The incident
On August 3, 2020, after finishing its salmon processing season in Alaska, the Aleutian Falcon docked at Trident Seafoods’ shipyard facility in Tacoma, Washington, to begin its maintenance and repair (M&R) period in anticipation of the 2021 processing season. During M&R periods, workers were assigned to the vessel; they came aboard in the mornings and left in the late afternoons. These workers usually included the chief engineer, port engineer, welders, and deckhands, who were all Trident employees.
[smlsubform prepend=”GET THE SAFETY4SEA IN YOUR INBOX!” showname=false emailtxt=”” emailholder=”Enter your email address” showsubmit=true submittxt=”Submit” jsthanks=false thankyou=”Thank you for subscribing to our mailing list”]
Additional laborers were drawn from local temporary employment agencies. One of the worklist items scheduled to be conducted during the M&R period was
to crop and renew a section of corroded steel bridge deck plating that measured 22 feet transversely and 20 inches longitudinally. The corroded section of plating ran beneath the aftmost transverse bulkhead on the port side of the house.
The lower portion of this bulkhead, near where it met the deck, was also corroded and needed to be cropped and renewed. The steel would be cut out using oxy-acetylene cutting torches and electric grinders with cutting wheels. The job was considered “hot work,” since these tools could produce sparks. After the corroded steel was removed, new steel plating would be fitted into the open area and the seams welded.
Beneath the bridge deck plating being removed, within the shelter deck, was a pantry, a dry stores area, and the forward section of an enclosed freezer space (also called the “walk-in refrigerator”). At the forward end of the walk-in refrigerator and inboard was a longitudinal insert about 4 feet long (hereinafter referred to as a “wooden bulkhead”) that separated the refrigerator space from the pantry.
This insert (which, according to the chief engineer, had been fitted sometime before 2012) was constructed of two-by-four wooden framing that had insulation between the wood and 0.5-inch plywood on either side, referred to as sandwich-style construction. Forward of the walk-in refrigerator was the dry stores area. Both areas contained rows of wooden shelving.
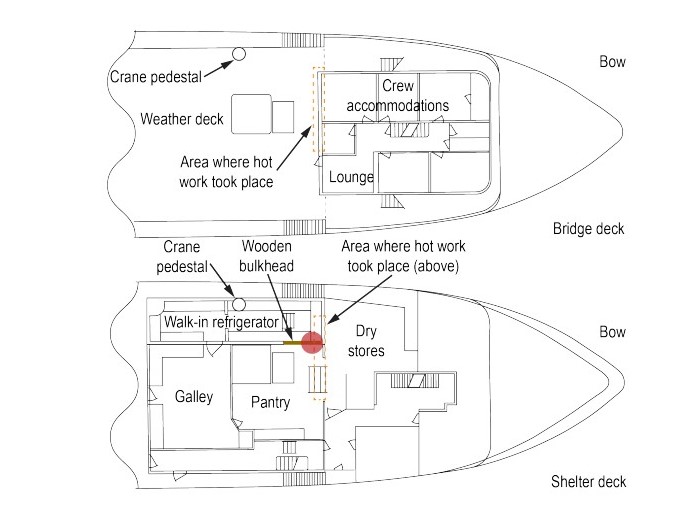
where the deck was being cut is highlighted with orange dashed lines. The area where the fire began on the shelter deck is indicated by a red circle. (Background Source: Trident Seafoods) / Credits: NTSB
The company’s vice president of safety stated that when hot work was planned around areas with foam, a marine chemist would typically come on board to “tell us the distance that we need to be able to…clear the foam out…or what we need to do to mitigate it.”2 On February 4, 2021, a marine chemist, accompanied by the company’s port engineer, surveyed the hot work areas where the cutting and inserting would take place.
The marine chemist stated that cutting through the bridge deck was not discussed; the port engineer, however, stated that he told the marine chemist that they
were going to cut and insert new plating in the deck. The marine chemist issued a marine chemist certificate, which allowed workers to “grind, weld, and cut with cut off wheel to the weather deck above the walk-in refrigerator (forward) without penetrating it” and required workers to “keep hot work 12 inches away and isolated from any foam insulation.” The certificate was signed by the port engineer. The port engineer told investigators that he did not believe they would be cutting into the walk-in refrigerator space.
On the morning of February 17, the port engineer discussed the assigned work to be completed that day on the Aleutian Falcon with the lead welder while ashore at the Trident office in Tacoma. At that time, about the lower 2 feet of the aftmost bulkhead and a portion of the deck plating on the starboard side had already been removed using cutoff wheels.
The workers planned to use cutting torches to finish cutting the section of bridge deck plating away from the steel supporting frames below it. The port engineer typically also discussed the planned work with the facility safety manager, who was also the shipyard competent person (SCP) for the Aleutian Falcon at the time, but he was not certain whether he had done so that day
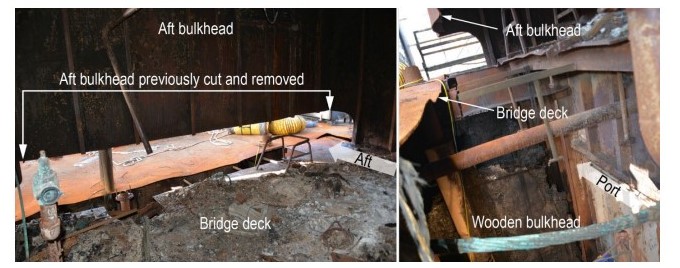
casualty (Background source: Bureau of Alcohol, Tobacco, Firearms and Explosives) / Credits: NTSB
Shortly after 0600, regular workers from Trident and temporary workers boarded the vessel. The workers included the supervisory lead welder, four welders, one laborer, and four fire watches. According to the workers, before the hot work began, they removed the polyurethane foam insulation and protective coatings (paint) in the area of the planned hot work and protected all combustible materials that could not be removed with fire blankets and fire suppression gel.4 Where flammable (combustible) items could not be removed in an area where hot work would be completed, fire blankets would be used to cover the area and jammed into cracks, after which they would be wetted.
The SCP stated that he and the lead welder walked through the Aleutian Falcon and inspected areas where hot work was to take place, including the walk-in refrigerator and dry stores area, to ensure that the hot work areas had been adequately prepared and that firefighting equipment, such as charged fire hoses and fire extinguishers, were readily available.
The port engineer stated that he believed he inspected the same areas to ensure that there was proper preparation before beginning hot work. Normally, the port engineer would also check in with the vessel’s chief engineer if the vessel was crewed, but the chief engineer was temporarily assigned to another vessel and was not aboard the Aleutian Falcon because the processor was out of service.
About 1230, a welder in the dry stores area began cutting the deck plate with a cutting torch that freed the plating from the frames below by burning through welds. Fire watches were assigned to monitor the hot work areas, including the pantry, dry stores area, and walk-in refrigerator (described by one fire watch as very tight to work in due to the presence of an overhead evaporator, which had not been removed from the space during the preparation for hot work). During the process of freeing the plating, a small fire broke out in a piece of plywood located in the dry stores area. The workers extinguished the fire and continued hot work.
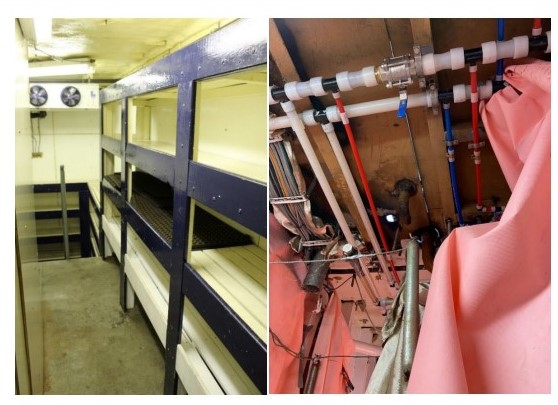
showing overhead evaporator, wooden shelving, and step-down area, and the dry stores area
(right), looking to port and overhead, containing draped pink fire blankets. (Source: Trident
Seafoods) / Credits: NTSB
After completing the torch work to free the plate, two welders on the bridge deck area began plate removal over the walk-in refrigerator area using cutting disks attached to electric grinders, cutting through the deck during the process. According to the workers, all cutting concluded about 1520. The fire watch in the walk-in refrigerator monitored the area until about 1620.
At 1631, he left the vessel; he was the last of the workers to leave the area where hot work had been completed. Trident employed the services of a security watch that made regular rounds of the facility. While the Aleutian Falcon was at the shipyard, the fire-detection system remained functional, alarming in the pilothouse if a fire was detected. Between 2122 and 2126, the guard walked along the pier where the Aleutian Falcon was moored but noticed nothing unusual.
At 2145, a motorist located across the Hylebos Waterway noticed white smoke coming from the Aleutian Falcon; he did not report the smoke because he believed it was the result of work being performed aboard the vessel. He kept driving but stopped further along the road at an overlook to observe the vessel, then noticing an orange glow in the area where he had earlier seen the white smoke. At 2232, he made a 911 call to report the fire.
At 2255, the Tacoma Fire Department arrived on scene. Firefighters reported there was no one at the gate when they arrived, so they were initially unable to gain access to the pier where the vessel was docked. Once they gained access to the pier, the firefighters “initiated access” to the vessel and saw fire “at the base of the pilothouse.” They first set up fire hoses to isolate the fire in the forward and midship areas where they could see flames, and an aerial ladder was supplied to “protect exposures and knock down bulk fire without boarding the ship.”
Shortly after the hoses were prepared, responders determined that fire conditions “would not allow for a safe land-based shoreside fire attack,” so they transitioned to a defensive strategy, cooling the hull using fireboats. Between 0402 and 1131 on February 18, a “shelter in place” order was issued to the local community due to the danger of smoke and toxic fumes carried by the prevailing winds. The fire was declared extinguished at 1300 on February 22.
Analysis
At the end of the fishing season in August 2020, the Aleutian Falcon docked at the Trident Seafoods facility to complete maintenance and repairs. No one remained (or lived) on board while the vessel was docked, but workers came on board during the day to perform tasks as assigned.
On February 17, 2021, workers planned to continue ongoing hot work by removing corroded steel deck plating located on the bridge deck above the pantry, dry stores area, and walk-in refrigerator. The plating was located beneath bulkhead plating above that had already been cropped out. Because the work was in an area that adjoined foam insulation below, a marine chemist had previously been brought on board to examine the areas involved. The port engineer, SCP, and lead welder (supervisory personnel) understood that replacing the wasted deck plating meant that that the old steel had to be both cut out and new steel welded in place.
Therefore, they should have been aware that the spaces immediately beneath the deck would be subject to flames, heat, and sparks from torchwork, grinding, and then welding. However, it is unclear whether the port engineer explained to the marine chemist that they would be cutting through the bridge deck plating. The marine chemist issued a certificate, signed by the port engineer, that stipulated that work must be completed “without penetrating” the bridge deck, indicating he either was not aware or clearly informed of the full scope of the planned hot work, or he wrote the stipulation in error. It is also unclear whether the port engineer or SCP noticed or whether the lead welder or workers were informed of the restrictions listed in the certificate.
The SCP was required by OSHA and the NFPA (as well as the company’s hot work policy) to complete a safety inspection of the area where hot work would be completed to ensure the space was adequately prepared. The SCP stated that he inspected the hot work area with the lead welder, and the port engineer believed he had inspected the spaces as well.
However, if either had performed a thorough inspection, they would have been aware that the planned work would involve cutting through the deck directly above the wooden bulkhead and foam insulation separating the walk-in refrigerator and pantry and then about 4 feet into the walk-in refrigerator itself, which would therefore violate the conditions of the marine chemist certificate. If the supervisory personnel were confused by the restrictions listed on the certificate (since the restrictions prevented the exact work they planned to complete), they could have requested clarification from the marine chemist, but none of them did so.
The marine chemist certificate required the removal of all foam insulation within 12 inches of the area of planned hot work—likely as a precaution in the event the foam was combustible and could create toxic fumes when exposed to heat from hot work nearby.
The workers stated that they removed the foam insulation in the area of hot work, including foam in the walk-in refrigerator, indicating that
- they believed the hot work would involve the walk-in refrigerator, and
- the workers were either aware of some of the requirements in the certificate or had been instructed to remove the foam by a supervisor.
However, the workers did not remove the foam-filled wooden bulkhead, which was combustible; instead, they covered the area in fire blankets and stationed a fire watch in the walk-in refrigerator. The wooden bulkhead was of sandwich-style construction, and based on post-fire photographs, the bulkhead reached to about the transverse steel framing members supporting the bridge deck and was not removed beneath the deck. This type of construction would have made it almost impossible to adequately protect the bulkhead without removing it completely.
Additionally, according to NFPA standards, hot work should not have been performed on this bulkhead because of its sandwich-style construction. While the lead welder should have been aware of the presence of the wooden bulkhead, there is no indication he communicated as much to the SCP or port engineer. Based on the damage to the vessel’s walk-in refrigerator and dry stores area, as well as the ATF’s preliminary findings, the fire’s most likely area of origin was near the longitudinal wooden bulkhead located forward in the walk-in refrigerator space, adjacent to the pantry, and aft of the dry stores area, located directly below the area where hot work had been completed for the day.
The hot work would have produced sparks and slag that likely traveled from the deck above (overhead) into the wooden bulkhead separating the walk-in refrigerator and pantry, igniting the combustible materials in the area, as well as the bulkhead, and allowing for a smoldering fire to become established.
Because of the fire’s location, it would have likely gone unnoticed by a fire watch before they departed the vessel about 1 hour after work was completed for the day about 1631. Once the fire developed further, it was likely detected by the vessel’s fire-detection system hours later; however, the system would have alarmed only in the pilothouse, an area that was unmanned at the time, so no one was alerted.
The shipyard had a security guard who walked by the ship at 2122, but he did not notice anything unusual. Because no one was aware of the fire, it continued to grow and spread, until it became large enough for a passerby to report it about an hour later. The delay in recognition allowed the fire to expand to a point that responding firefighters could not enter the vessel, and the Aleutian Falcon was extensively damaged above the waterline.
Conclusion
#1 Probable cause
The National Transportation Safety Board determines that the probable cause of the fire aboard the fish processor Aleutian Falcon was the company’s supervisory personnel inadequately planning for hot work, as well as shoreside workers’ inadequately protecting hot work areas, allowing slag from hot work to ignite combustible material near an insulated wooden bulkhead of a walk-in refrigerator that had not been removed or sufficiently protected. Contributing to the casualty was the ineffective communication between the supervisory personnel, marine chemist, and workers.
#2 Lessons learned
It is critical for supervisory personnel to evaluate hot work areas for fire hazards to ensure that affected spaces are completely understood, prepared, and protected for planned hot work in accordance with regulatory guidelines, company policies, and marine chemist certificates. Adherence to proper policies and procedures is vital to completing a safe hot work operation. Additionally, crewmembers and personnel involved in hot work should be able to identify hazards and take action to remove or mitigate potential risks to the vessel.