U.S. Coast Guard addresses the importance of verifying the condition and electrical duty ratings of the motor starter contactors in the winch controller for lifeboat and rescue boat launching appliances, and provides lessons learned.
The incident
An offshore operator experienced a failure during routine maintenance and recovery of a rescue boat on one of their facilities where the electrical motor
contactor for the winch motor failed in an energized position (i.e., motor in an “on” or “hoist” condition).
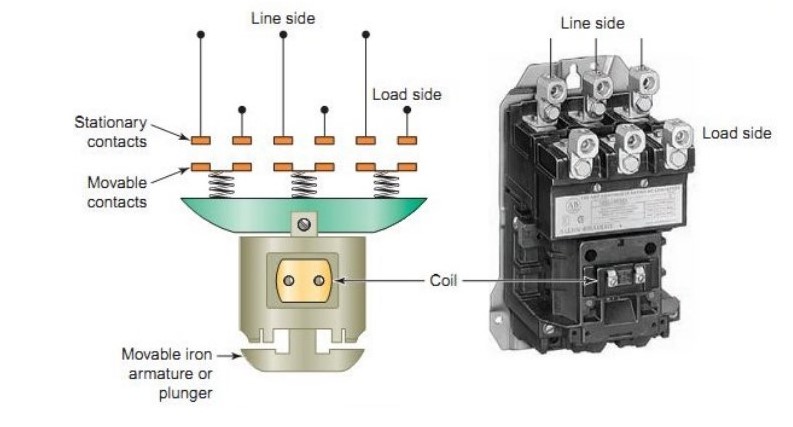
This failure occurred when the contactors fused together due to exceeded duty rating. Metallurgical/post-event analysis ruled out any other failures with the contactor. The hoist button, emergency stop (E-Stop) and limit switch circuits all failed to stop the winch from hoisting. The operator’s personnel were able to secure electrical power via the 480-volt main breaker at the winch controller before the boat contacted the davit, avoiding serious damages and injury to personnel.
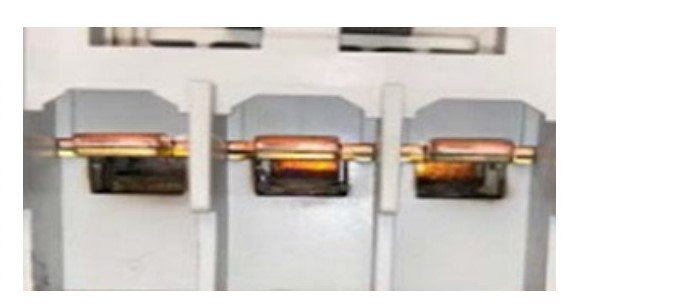
In this particular davit controller design, the 120-volt control circuit engages and disengages the 480-volt motor starter that powers the winch motor. The “winch up” control button, EStop, and the limit switch interrupts the 120-volt control power to the starter. In the described incident, all three devices interrupted the 120-volt control power, but 480-volt power continued to the winch motor due to the welded starter contacts.
Probable Cause
Further analysis by the facility operator found that the contactors were not rated for intermittent cycling (start and stop sequences) of the winch and the contactor manufacturer had issued technical guidance on the issue of welded contacts. The operator issued an internal alert, inspected the contactors in the winch controllers on their other facilities, and found several contactors that had evidence of overheating and indications of welded and scorched contacts.
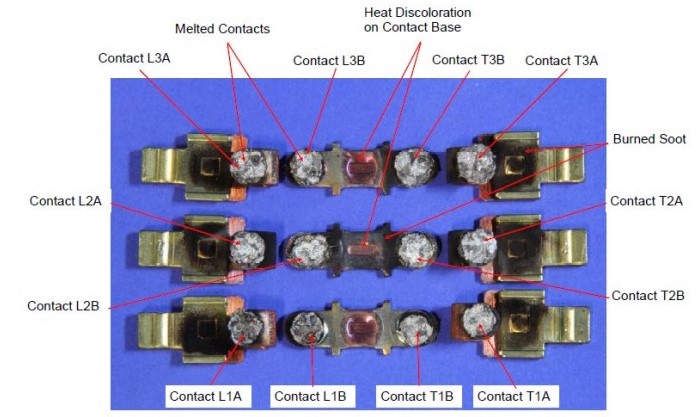
Intermittent cycling is a common practice during recovery of a lifeboat or rescue boat into the stowed position. A winch may be cycled after the boat has cleared the water to verify release gear condition prior to continued hoisting, possibly cycled several times during long hoists to reduce pendulum motions of the boat (for vessels, mobile offshore units or facilities that do not utilize a painter line during boat recovery) and cycled at approach to davit guides/stops.
While commonly employed for a safe recovery process, intermittent cycling may exceed design and duty ratings of the electrical components.
Several launching appliance manufacturers were contacted to inquire into electrical/control component selections (duty ratings) that may not be specifically addressed by equipment type approval requirements, awareness of contactor issues (welded contactors) in their controllers and awareness of contactor manufacturer documentation related to exceeding the duty ratings.
While limited information was received, component selection and design mitigations to prevent exceeding duty cycles did vary by manufacturer and, although a rare occurrence, two manufacturers were aware of incidents involving welded contactors in their davit controllers.
Lessons learned
The Coast Guard strongly recommends that owners, manufacturers, operators and service providers, do the following:
- Verify condition of winch motor contactors and replace any contactors that show signs of excessive wear, overheating, or welding;
- Verify the duty cycle ratings of lifeboat and rescue boat davit electrical components and compare those ratings to recommended and commonly-practiced boat recovery procedures/processes;
- Verify the design of the davit safety devices (i.e., E-stop and limit switches) to see if they will secure electrical power to the motor in the event of welded contacts;
- Implement training for all personnel that operate the davits to ensure awareness related to electrical duty cycles and actions to isolate power in the event of a welded winch motor contactor.